Background
A company engaged in the production of semiconductor raw materials is concerned about their over heating problem in one of their low voltage switchgears. The heat was so intense that they were forced to shutdown to remove melted current transformers and prevent catastrophic equipment failure and longer downtime.Situation Analysis
A thermographic inspection was conducted to determine the cause of the over heating problem. Figure 1 shows the result of thermographic inspection.
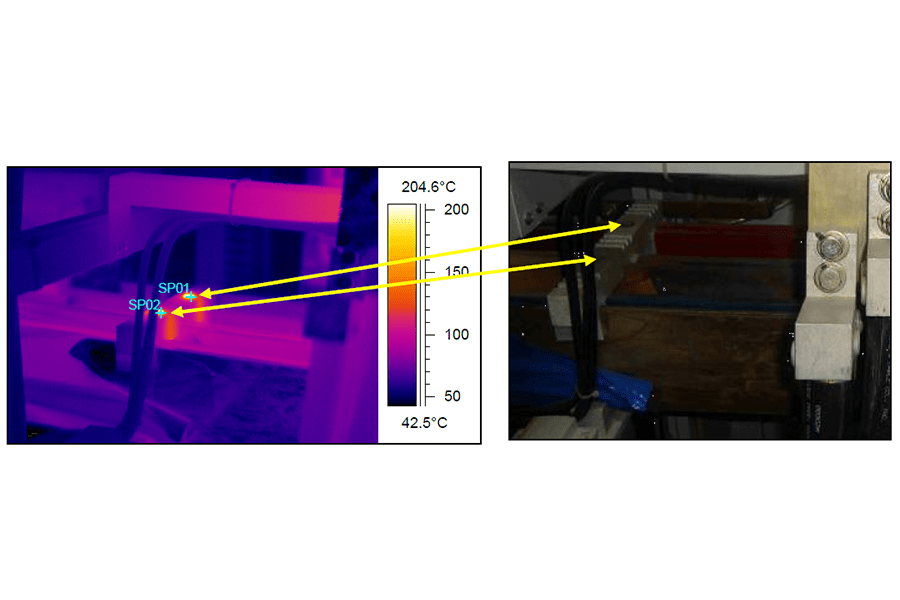
Figure 1. Infrared image of the overheating component/bolts inside the low voltage electrical panel
Here are two possible causes of the bolt’s abnormal heating. One is due to vibration (because of loose connection). The second is due to induction.
Loose connections could easily be remedied by re-tightening of the bolts during scheduled shutdown or preventive maintenance. The heating due to induction could be prevented be replacing the existing bolts with non-ferreous or non-magnetic bolts.Solution
During the company’s scheduled preventive maintenance, it was found out that the bolts were tightly secured in place. To prevent the overheating, the old bolts and busbar support were replaced with phenolic boards attached to a beam above the busbar (See Figure 2).
The overheating problem was resolved and the company was happy with the solution.
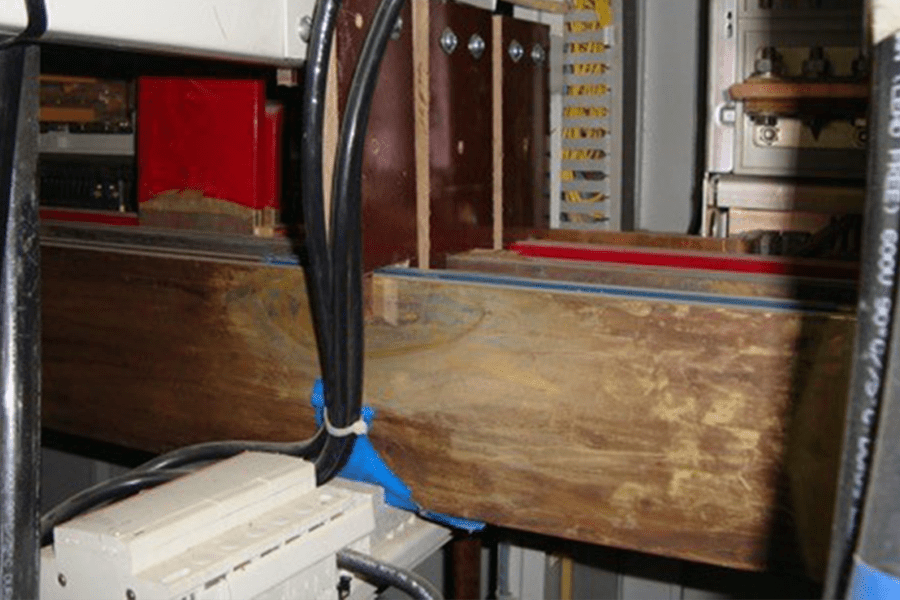
Figure 2. Old busbar support and bolts were replaced with Phenolic Boards attached to a beam above the busbar